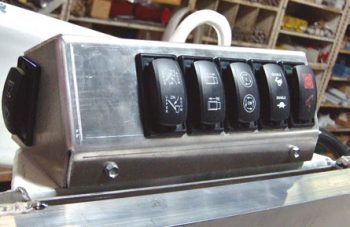
An Armstrong maker of hydraulic lift vehicles expects to save money and eliminate production delays after CIRAS helped the company find an alternative for a problem part.
TG Industries, which also does business as Arm Lift, started using a particular type of rocker switch in its vehicles in 2000, said engineer Loren Kinnander. By 2019, the once-standard switches were no longer common. Prices rose as they became harder and harder to obtain from the company’s single overseas supplier.
Kinnander said the company regularly would purchase four to six months of switches at a time and “hope we’d get the next batch before we ran out.”
Chris Hill, director of the CIRAS Technology Assistance Program (TAP), ultimately helped TG Industries rethink its product design. CIRAS used a 3D printer to create new adapter flanges for the switch—prototypes that the company then could test in existing products.
Arm Lift now uses a new Iowa-produced plastic adapter alongside easier-to-get rocker switches. Kinnander estimates the changeover’s total benefit ultimately will top $150,000—including lowered costs, reduced downtime, and an expected increase in sales.
“It really worked out quite well,” he said. “I’m kind of excited.”
For more information, contact Chris Hill at chhill@iastate.edu or 515-313-8251.
A version of this article was published in the Winter 2021 edition of CIRAS News. To read more of that edition or others, please explore elsewhere on our website.