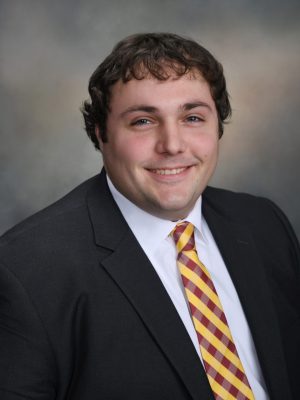
It’s a common misconception among many manufacturers that assisted and augmented reality (AR) technology are outside their reach – mystical, gimmicky technology that really has no place on their production floor.
These technologies are portrayed as “space-age” bits of hardware and software that certainly cost a fortune and probably require a rocket scientist to operate. We understand the mindset, but in reality, this couldn’t be further from the truth.
Let’s break it down.
What the Terms Mean
There are a lot of terms thrown around leading to some confusion, so let’s make sense of it all:
Assisted reality is the most basic technology and involves projecting key 2D information into your view to aid in a task. Think heads-up displays on cars, where information is projected seamlessly onto the windshield. Or, your alarm clock projecting the time and date onto your wall when the alarm sounds. Yeah… that’s technically assisted reality.
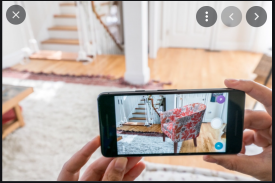
Augmented reality is essentially the same thing as assisted reality, but it differs slightly in that the projected information is displayed in 3D. WayFair utilizes AR on its website to help customers understand, before it’s bought, how furniture will look in a particular room.
In manufacturing, think about using this type of technology to ensure that equipment can be moved easily and installed in the desired location, thereby addressing any concerns ahead of the actual move.
Virtual reality (VR) is where we start to enter a world more closely resembling science fiction. With VR, the user is completely “immersed” in a virtual environment. This is where you start seeing the full-face VR headsets, such as those used in video games and with 3D virtual tours.
As you move from assisted, to augmented, and then to virtual reality, the barrier to entry grows. Some assisted reality solutions are plug-and-play. Augmented reality requires more work to get started, as you’re going to also need 3D information to feed into it. This requires 3D CAD models for anything you want to be projected into a user’s view. Lastly, virtual reality setup and programing can be resource-intensive to develop if you aren’t purchasing pre-packaged solutions.
How You Can Use it
Now that we’ve demystified some of the terms, let’s talk about what’s important. How can these be used as tools in manufacturing? For simplicity, moving forward we’ll use the term “AR” for both assisted and augmented reality. (Recall that the only difference is if we’re projecting 2D or 3D information.)
Since AR has a much lower barrier to entry than the other technologies, we recommend that this be your first foray into the space. Use-cases such as remote assistance are a great example of how you can take hardware you already own (smartphones, laptops, desktop PCs) and use them to remotely serve customers, support field technicians, and “be in the field” without being in the field. There are numerous available software packages, and we have several in our Digital Manufacturing Lab to demonstrate the technology. We can show you some fantastic options to have one-on-one technical calls with anyone in the field who has a smartphone.
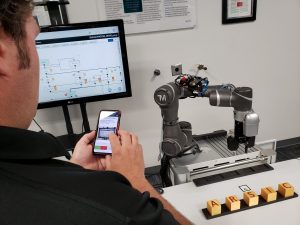
These remote assistance solutions allow you to share video and audio feeds with enhanced functionality, such as integrated document sharing, session recording, and live 3D annotations. This added functionality makes these tools far superior to standard video calls for technical communications because it provides for more precise communication between an expert and a field user.
AR can also support your workforce training efforts. Guided work instructions consist of a workflow of instructions used to navigate someone through a task. Instructions are displayed to the user via a display screen (TV, tablet, laptop, smartphone, or monocular AR headset) in a step-by-step fashion to train them, ensure the quality of their work, and track their progress. They can even be integrated into your other systems.
These types of instructions are extremely valuable in maintenance and assembly tasks where you might have a high mix of parts, complex assemblies, high turnover rate, tasks completed infrequently, or a need for greater quality control.
Complexity Comes with Concerns
In terms of ease of integration, virtual reality requires a thorough plan for implementation. Systems that include full-face hardware may raise serious safety concerns on a dangerous shop floor. Virtual reality applications might require more specialized hardware, and building VR modules can be extremely resource intensive. For these reasons, we typically focus on pre-built training modules for manufacturing environments. Training applications for welding can provide significant advantages to your training efforts.
We hope that you see some of the uses on your own production floor and how these technologies can make your workforce more productive, as companies struggle to find employees.
Come to our Digital Manufacturing Lab to see how some of these technologies could support your improvement efforts. CIRAS is always available to help you find the solution that’s right for you.
For more information, contact CIRAS Project Manager Jake Behrens at jbehrens@iastate.edu.