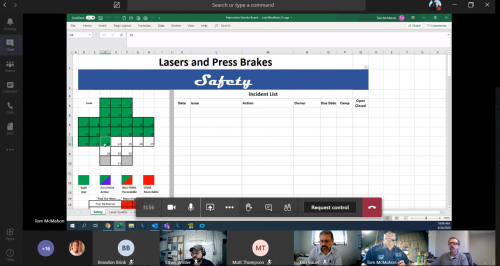
A Garner-based maker of hydraulic truck equipment has found an unexpected benefit to pandemic-imposed limitations on its factories – by taking a valuable Lean management tool online.
Brad Tiedemann, manufacturing engineer manager at Stellar Industries, said the company discovered more efficiency and smoother problem solving after COVID-19 restrictions forced Stellar to create an alternative to the company’s daily gemba walks.
Gemba, a Japanese term for “the actual place,” is a major tool in Lean management. The practice involves daily factory tours by company managers to view visual information about business performance. Leaders then can spot problems quickly and coordinate to find solutions.
But how do you do all that while maintaining social distancing?
Bowing to reality, Stellar canceled its gemba walks in March after the pandemic hit. But floor managers were unwilling to completely shelve the progress Stellar has made since it first adopted Lean in 2018. So, in what the company credits as a true example of its burgeoning Lean culture, Stellar quickly decided to take its gemba walks virtual.
“It’s a great example of problem solving from all levels of the organization,” said Tracy Schuster, director of the Iowa Lean Consortium. “It is an example of how Lean thinking helped them.”
The gemba walks that used to draw five or 10 managers now regularly involve more than 125 virtual walkers as part of a daily Microsoft Teams meeting. Twenty Stellar managers at six factories in Garner, Kanawha, and Hastings, Nebraska, take turns sharing spreadsheets with the latest statistics covering safety, quality, and delivery.
Tiedemann said the change already has proven so useful that the company has decided that virtual walks will survive the pandemic. Managers at one factory now routinely spot problems at another and share tips via phone calls once the virtual meeting is over.
“I don’t see us ever getting away from this,” he said. “There’s just too much benefit from having everybody see everything.”
Tiedemann acknowledges that he misses walking the actual factory floor and observing workers in the act. But they’re working on ways to get that back into the process once COVID-19 is no longer a concern.
“I do think we’ve lost something by not being on the floor,” Tiedemann said. “But I think we’ve gained so much more.”
For more, contact Tracy Schuster at tschust@iastate.edu or 515-715-0164.