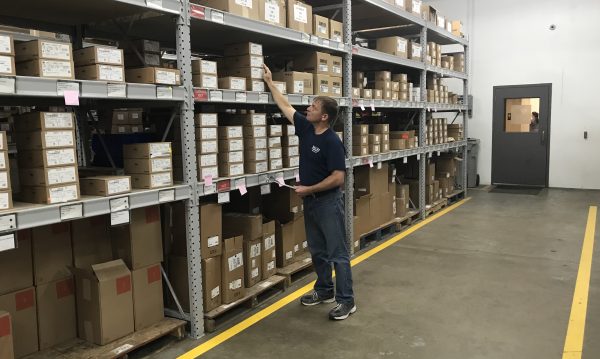
A Des Moines commercial door and security company improved efficiency and shaved roughly $200,000 off its costs after CIRAS assistance helped the company upgrade its inventory handling.
Dave Hunt, hardware inventory control manager for Walsh Door & Security, said his company went from carrying roughly $600,000 worth of door hardware at its Des Moines warehouse to roughly $430,000. The difference was made possible by a 2017 CIRAS class that helped Walsh become more professional about calculating what the company really needed on hand to meet its customers’ needs.
Before attending the CIRAS Inventory Management 101 class, “I didn’t know the different ways to calculate inventory, the value of the inventory on the shelf, or the cost of it sitting on the shelf,” Hunt said. “I also didn’t have an understanding of how many times we turned our inventory.”
CIRAS project manager Marc Schneider, who taught the 2017 class and later worked individually with Hunt, helped Walsh Door & Security understand how to calculate the minimum amount of stock required and set appropriate targets.
Schneider, who is teaching another Inventory Management 101 class on August 26, said many Iowa companies manage their inventory levels just fine – until they grow to the point that the old way of doing things doesn’t work anymore.
“I think in Iowa, and probably everywhere, a lot of small and medium-sized companies don’t really have a lot of formal training in managing inventory,” Schneider said. “They just kind of wing it.
“That’s OK when things are small, when you can manage things by looking at it and counting it,” he said. “But as these companies start to grow and have more volume, they find it harder to do all of this and just manage it in their heads. They realize that they need to have a more formal approach.”
Hunt credits CIRAS, along with a new computerized dashboard that helps Walsh Door & Security keep a better eye on its current stock, for helping the company become much more efficient. As one example, he cited a Schneider suggestion that the company change the way it orders supplies for major door installation projects. Instead of being ordered and placed into stock, locksets needed for those jobs now are ordered shortly before they’re needed and kept separate.
“It saves time for our hardware team,” Hunt said. “Because they don’t have to put it away and re-pull it later.”
For more information about inventory management, click here or contact Marc Schneider at maschn@iastate.edu.