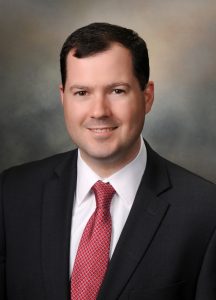
CIRAS Program Manager
Iowa is out of people.
Almost every company I talk to, regardless of size, industry, or location, says that finding good people is their number one issue. The few exceptions are expert Lean practitioners—such as members of the Iowa Lean Consortium (ILC)—who tend to look at the issue differently: If every single person in our business was better at seeing, communicating, and solving problems, they ask, wouldn’t it help our workforce needs?
Twenty-plus years ago, when the world began to interpret the famed “Toyota Production System” as magic tools necessary for everyone to cut costs and compete globally, most of us missed the point. In reality, the secret lies not in the tools but in the people that developed the tools and how Toyota developed those employees.
The truth is that Lean tools were never magic. Lean, when it’s done well, is hard.
But it works.
Lean is about leaders leading—developing people, helping them see waste, and providing them with the coaching, tools, and authority to fix issues themselves. None of this is expensive or time consuming, but it requires real effort and behavioral change at every single level of your organization.
The most recent CIRAS study of manufacturers’ needs shows that despite Iowa’s workforce shortage, only about 20 percent of our manufacturers have fully embraced a productivity system. I see it as our responsibility to help Iowa manufacturers see the path in which developing people and simplifying processes helps them get more product out the door with the same staff.
This is one of the many reasons why I’m so excited that the ILC joined CIRAS last summer. Together, we’re going to be working closely in the coming months to define the next generation of Lean in Iowa. That will mean more resources for current ILC members and new options for the thousands of companies out there that need people and have not yet embraced Lean.
> For more information, contact Mike O’Donnell at modonnll@iastate.edu or 515-509-4379.