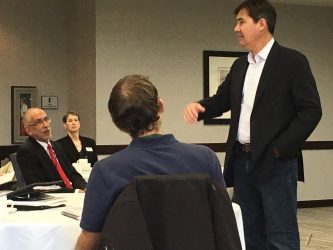
“Do you bail, or do you paddle? The answer is that you have to bail, and you have to paddle,” Lancaster said. “You don’t get to have a philosophical discussion about what’s more important. You have to do both.”
“Figuring out how to do that in a business that’s growing – and prioritizing that, if you’re the senior leader – that’s the real challenge.”
Lancaster, CEO and owner of Lantech.com LLC in Louisville, Kentucky, was the speaker at this year’s CEO Power Breakfast, part of the ILC’s annual Fall Conference in West Des Moines on October 24. Lantech was one of the first American companies to implement Lean manufacturing techniques. The firm makes packaging and material-handling machinery, including stretch wrappers, conveyors, and case forming machinery.
The company has worked diligently over the years to accumulate and hold its competitive advantages, Lancaster said. But that can all be lost quickly.
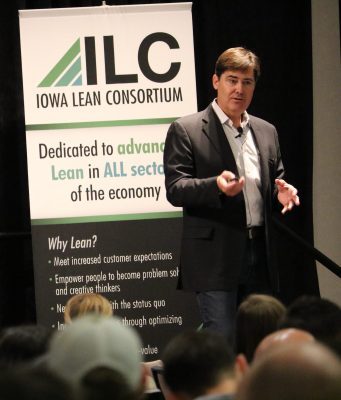
He described visiting the company’s Netherlands operation shortly after a factory move and finding a fouled-up production operation. Newer employees, not as experienced with the reasoning behind Lean manufacturing processes, had accidentally thrown the plant into chaos when they abandoned a two-bin system used to control the flow of parts for work in progress. The workers thought they were helping to save space in the new location.
Older workers, who had labored to improve the original process, understood how the two-bin system helped speed production.
“But we lost the underpinning of ‘why’ as we went through the generations of people and the company grew,” Lancaster said. “So, when we threw a big bomb of change in there, the implementation changed. As people tried to optimize and keep us going, as they tried to do the right thing, they made compromises to get things done, not understanding the ramifications.”
Lancaster urged the breakfast attendees to get out and look at what is happening on their shop floors so they can understand how work really takes place. That’s the only real way to diagnose a problem, he said: “As you grow and you have executives working for you, boy is it easy to sit and talk – pontificate about what the problem could be.”
“Golly, it’s hard” to diagnose a problem, Lancaster said, briefly acting out one side of a conversation with imaginary underlings before moving toward an imaginary shop floor. “ ‘Yep, that’s interesting.’ ‘That’s interesting.’ ‘Now, follow me.’ ”
Lancaster urged executives at the breakfast to adopt a philosophy focused in improving the lives of their workers. Production-level employees are the only ones who actually make the company money, he said, referring to anyone outside the production line as “blood-sucking overhead.” Bosses should work their hardest on removing obstacles and getting people the correct tools and training they need to succeed.
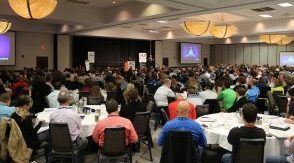
“I think being a manager is one of the most important jobs anybody can ever have,” Lancaster said. “Being a manger effects how people live their lives dramatically. You can impact as a manager whether folks go home tapping their fingers on the steering wheel, or whether they go home frustrated and mad – and that impacts how they parent, what kind of spouse they are, how they interact in the community, et cetera, et cetera.”
“The number one thing is: Don’t frustrate your people,” he said. “Challenge your managers to go around solving problems for their people…. The only way we can make money is if we can help the people in line be more effective than they could be on their own.”
Next year’s Iowa Lean Consortium Fall Conference will be held October 29-31 at the Sheraton West Des Moines.
For more information, keep an eye on www.iowalean.org under “Learning Opportunities.”