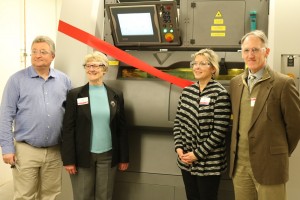
The new machine, part of a $900,000 investment CIRAS made last fall to help educate Iowa businesses on the benefits of metal additive manufacturing, arrived on the Iowa State campus in October and had been used to help with more than a dozen company projects over the past several months. But Thursday, Feb. 11, was the first general demonstration of the machine for the benefit of CIRAS’ clients, stakeholders and the public at large.
“This is a game changer,” CIRAS Director Ron Cox told a reporter from WHO-TV in Des Moines. “It allows you to design new products, new ways of doing things.”
The machine, a rare metal version of the increasingly common plastic 3-D printers, was purchased last October with a combination of money from CIRAS, the College of Engineering, the Iowa Economic Development Authority, and the federal NIST Manufacturing Extension Partnership.
The technology involves powdered metal and a laser that’s used to melt it, basically welding the dust into shapes orchestrated by a complicated computerized design. Building one 40-micron-thick layer at a time, the machine can produce any metal part or mold that can fit into a build envelope that’s slightly smaller than 10 inches by 10 inches by 12 inches.
CIRAS believes metal additive manufacturing is poised to change the way companies make and design almost anything. Geometric limits imposed by the production process are going to disappear. Manufacturers will be able to produce parts and products with less material and in days instead of the traditional weeks.
“Everybody has to change their way of thinking about how to make things work,” explains Jim Johnson, chief operating officer at Frog Legs Inc. in Ottumwa. “Otherwise, there will be some companies who change and take all the business.”
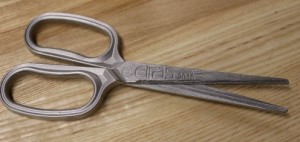
Johnson’s firm is one of several Iowa companies now working with CIRAS experts to explore the intricacies of metal additive manufacturing. CIRAS, by helping companies experiment and test the boundaries of this technology, hopes to help Iowa businesses prepare for some projected rapid growth.
“Is this technology ready for everyday use? No,” summarizes Chris Hill, head of CIRAS’ technology assistance initiatives. “But if I as a manufacturer can start getting educated now, then I kind of know what I can do with it. And when the technology gets a little better, then I can take advantage of it while my competitors are still thinking, ‘OK, now I need to start learning about this…’ ”
Attendees at last week’s event learned a great deal about CIRAS’ efforts to learn the intricacies of metal additive manufacturing – and the plan to share that information with Iowa companies.
Here are a few of the highlights from the machine’s coming-out party:
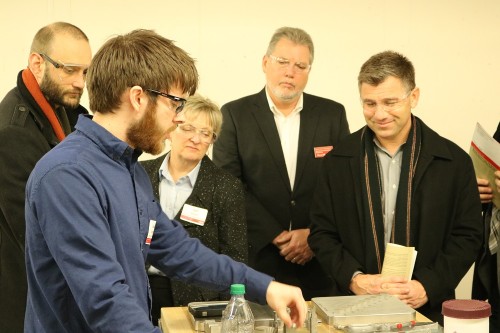
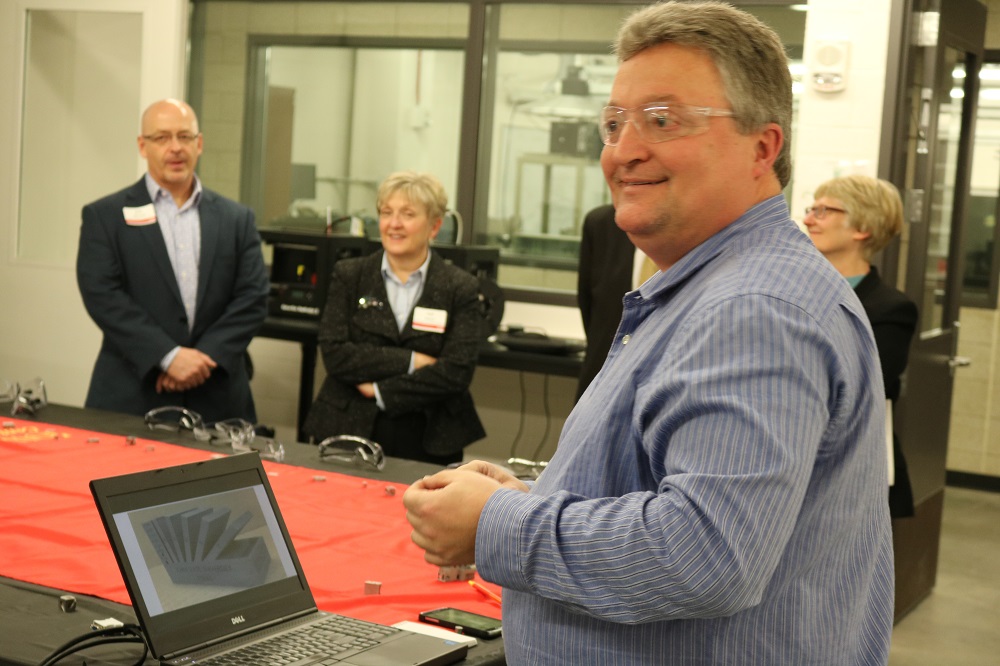
The myriad parts on display included two examples of what’s possible with metal additive manufacturing. The part on the right shows the way manufacturers currently have to drill cooling channels into molds for plastic parts. The straight line means water running through the outside of the mold will cool the plastic on the inside unevenly. But when molds are 3-D printed, it’s possible to create curved cooling channels that follow paths you would never be able to drill.
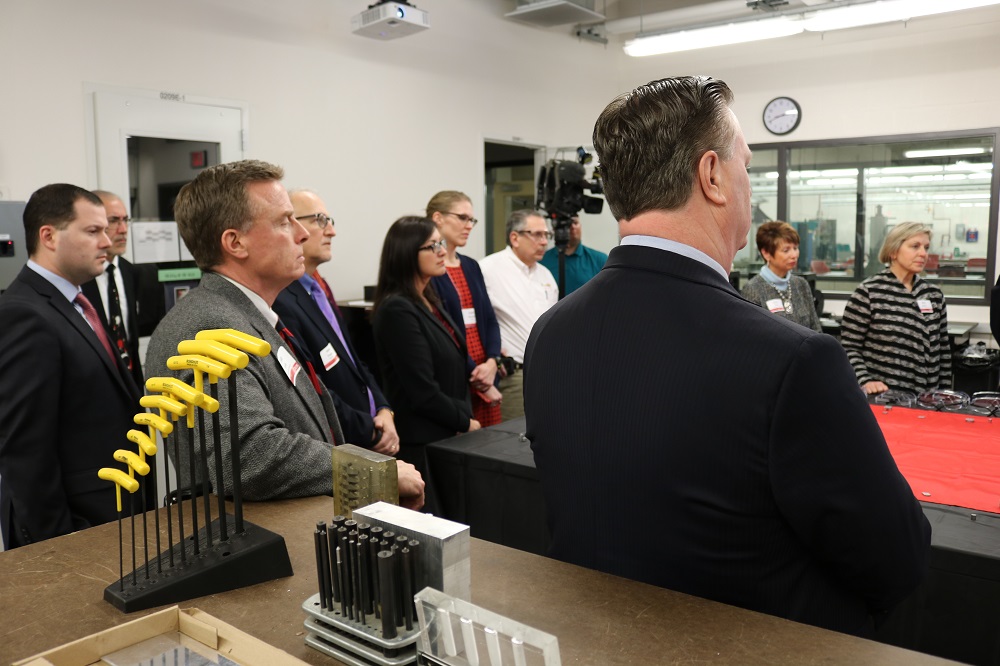
And of course, the media attended….
CIRAS would like to thank all the reporters and photojournalists who took time out of their day to help us educate Iowans about metal printing. For more information about what you’re planning you can delve more deeply into CIRAS Newswire, as well as read the last week’s fine coverage, including:
- An excellent front-page story on the Feb. 15 edition of The Des Moines Register
- A related gallery of Des Moines Register photos.
- This fine piece by Vanessa Peng and Spencer Vaughn of KCCI-TV 8 in Des Moines.
- A web story from WHO-TV 13 in Des Moines, which went up at the same time this short video aired:
- And statewide, a Valentine Day’s story published in the Waterloo-Cedar Falls Courier.
Many new Iowa companies have contacted CIRAS to inquire about the machine since the media coverage began. If you want to want to know more about the metal printer and what additive manufacturing might mean to your business, call Chris Hill at 515-294-5416 or chhill@iastate.edu.