Stronger manufacturing processes and new materials are anticipated to help Groschopp Inc. retain more than $800,000 in sales and save its customers $50,000 annually through avoided repairs.
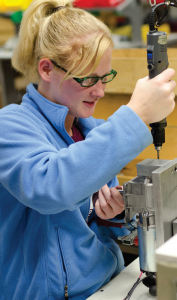
Groschopp’s Sioux Center, Iowa, manufacturing facility. (Special to CIRAS)
Groschopp, which is based in Sioux Center, Iowa, manufactures fractional horsepower electric motors to complete a variety of low-powered tasks. The company’s products include a full line of AC, DC, brushless, and universal motors, as well as right angle worm, planetary, right angle planetary, and parallel shaft gearboxes.
Groschopp was seeking to improve the quality and reliability of one of those gearboxes when it recently sought help from CIRAS, Iowa State University’s Materials Analysis Research Lab (MARL), and IPRT Company Assistance (IPRTCA), a longtime part of Iowa State’s now-reorganized Institute for Physical Research and Technology (which formally became part of CIRAS in July 2014).
The gearbox in question is integrated with a motor, and this gearmotor is attached to a vehicle transmission. Groschopp identified a gearbox component that was drying out the gear grease and changed this component by adding oil. The oiled prototypes solved the dry grease issue, but Groschopp sought help from CIRAS after the change caused a reduction in gear life.
CIRAS connected the company with IPRTCA, which used sophisticated laboratory equipment to conduct a metallurgical analysis on the gearbox’s worm shaft and mating gears.
“The goal of this specific project was to better understand the ideal shaft material and heat-treat combination that would consistently handle the life requirements,” said Scott Lundquist, a design engineer at Groschopp and an Iowa State alumnus.
The metallurgical analysis verified that Groschopp had received the correct gear materials from suppliers. But experts found that manganese sulfide stringers— molecular additives used to improve the shaft’s machinability—also had created microscopic weak spots on its outer surface. Essentially, the heat-treatment layer that was used to make the part’s surface harder was spalling, or falling off.
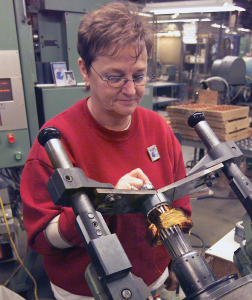
used in vehicle transmissions.
Adam Boesenberg, who did the testing at Iowa State, recommended Groschopp consider using alternative materials—ones without the molecular inclusions— to improve the part’s consistency. Groschopp now is working with its heat-treatment vendor to improve the lifetime quality and reliability of its gearboxes. “We’re primarily using the results to find a better material or better heat-treat process, or a combination of both,” Lundquist said.
Lundquist said the project will improve Groschopp’s relationship with its customers. He expects the company to retain $800,000 in annual sales due to the research and changes that the company will make.
In a separate project, Groschopp asked CIRAS and MARL to analyze electric motor parts and recommend improvements to extend the overall life of an electric motor brush. According to Paul Ross, commercial engineering manager at Groschopp, the company theorized that either external airborne contaminants or contamination from something inherent to the manufacturing process was causing brushes to wear inconsistently.
MARL’s researchers analyzed Groschopp’s brushes and commutator with an electron microscope. Ross said the testing helped eliminate some suspected contributors to the brush’s wear, increased Groschopp’s awareness of materials used, and sparked more training for operators handling materials on the factory floor.
“CIRAS was a big help,” he said.
For more information, contact John Roberts at 515-294-0932 or jarobert@iastate.edu.