Ryko Solutions, based in Grimes, Iowa, describes itself as the “largest manufacturer of managed car wash systems in North America,” selling various forms of rollover car wash systems to gas stations, convenience stores, car dealers, and private entrepreneurs across the continent. One of the company’s newest products (it launched in October) is the patent-pending CleanFill chemical concentrate management system. Until now, the car wash operator, owner, or manager had to find a machine, hire a service, or simply summon the brawn necessary to lift 5-gallon buckets or 15-gallon drums to refill the car wash chemicals. Ryko’s new system changes that by shrinking the size of refill containers to 2.5 gallons.

“Instead of having to move around something that’s 50 or 150 or 300 pounds, the operators can manage a jug that weighs 25 pounds,” said David Simpson, engineering manager at Ryko.
But before the system could use smaller jugs, Ryko needed to develop a special plastic funnel to place atop its large chemical holding tanks so customers could avoid chemical spills. The funnel also needed to have a mechanism to pierce the jugs’ foil seals.
Ryko created an initial design, but the company also wanted to get parts more quickly than normal for developmental testing. Ryko primarily fabricates its car wash machines from aluminum, stainless steel, and carbon steel, but it sought to use rapid prototyping for this project—something not usually done for sheet metal products.
Enter CIRAS.
Chris Hill, CIRAS project manager, helped Ryko navigate the world of rapid prototyping services—from suggesting alterations to improve the part’s design to creating the prototype.
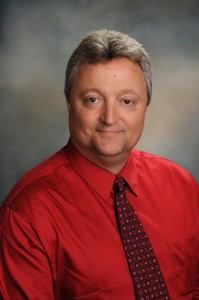
“Additive manufacturing, sometimes referred to as rapid prototyping or 3-D printing, is a method that uses 3-D CAD geometry and various types of technologies to build a part layer by layer,” Hill said. “A technology, typically a laser, is used to cure each layer of material. Using these methods, you can produce very representative and functional parts very quickly.”
To prove out the design, Ryko evaluated the full-scale prototype and tested it—then made a few alterations and tested a second prototype.
“We were able to use 3-D printing to create several design iterations on the receiver unit at full scale to evaluate and field test,” said Simpson. “What this then allowed us to do was settle on a final design before making the investment in the injection mold tooling. Ryko had never done this before, and through our working relationship with CIRAS, we found out they could be a resource to make this happen.”
Simpson estimates that Ryko saved three to six months of development time by using rapid prototyping. The company was able to unveil its 3-D prototype at a trade show and start taking orders several months in advance of the product launch date.
New sales from the funnel are expected to top $2 million in 2015. Additionally, Ryko is investing $1 million to upgrade customers’ dispensing equipment on-site and to acquire manufacturing equipment for injection mold tooling and automation. The new product also is helping boost business at two other Iowa companies—Innovative Lighting Inc., of Roland, and Product Development Partners, of Newton—that Ryko uses to supply its tooling and molding parts.
And the impact doesn’t stop there. CIRAS already is helping Ryko with a second design project using rapid prototyping, this time for a plastic cover so the funnel can be used outdoors or within car wash bays that are exposed to the elements. This product is expected to create an additional $400,000 in new business for Ryko.
For more information, contact Chris Hill at 515-294-5416 or chhill@iastate.edu.