Nestlé Purina, a manufacturer of dog and cat food and treats located in Clinton, was ready to address some long-standing factory improvement needs. They chose a path that has proven beneficial for many CIRAS clients: a capstone project involving Iowa State University College of Engineering students.
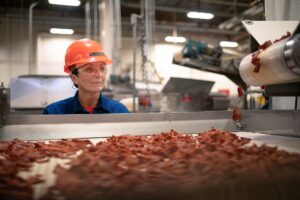
“Having new perspectives to review our processes was beneficial, as it allowed us to dedicate time to thoroughly examine our methods and identify gaps,” said Chris Sheridan, manager of specialty pet processing at the Nestlé Purina facility in Clinton. “This partnership proved advantageous for both the factory and the students providing an opportunity to explore potential solutions.”
This year, the company completed two College of Engineering capstone projects with student teams from the industrial manufacturing and systems engineering (IMSE) program. The teams visited the factory to experience the issues firsthand, studied historical data, and conducted various analytical studies.
One IMSE team worked on improving efficiency on a problematic small packaging line. Bags filled with dog and cat food were tipping over, resulting in production stoppages and wasted products. The students recommended changing the height of a platform and adding a support arm to prevent bags from tipping over and stopping the line. The team’s recommendations reinforced Nestlé Purina’s mission to care for its team by suggesting a guard around the filler to improve safety. Additional recommendations included collecting data on centerline runs to determine optimal operational settings, adjusting some conveyor joints where the bags were getting stuck, and angling a conveyor flat plate to help avoid bag “beaching.”
The student team estimated a $3.1 million impact through enhanced production capacity and reduced product loss.
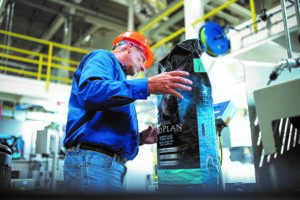
“We implemented the students’ ideas from the small bag line project, including guarding changes recommended for team safety,” said Justin Wilkinson, Nestlé Purina factory manager. “Their fresh perspective is making our operations run more efficiently.”
Another team focused on a production line for dog treats like Beggin’ Strips and Prime Meaty Bits. The line was experiencing frequent stoppages between the processing and packaging departments, resulting in extra costs, lost production time, and product waste. The goal was to reduce stoppages by 10 percent.
After analyzing several options for efficiency and return on investment, the IMSE students recommended removing a hopper and installing a monitoring system. The recommendation would achieve the 10-percent stoppage reduction goal, increase production, and decrease product loss.
“Our engineering department is currently working on designing the future conveyance system for the treats department, effectively integrating the information from the capstone team to enhance the efficiency of the future design,” said Sheridan.
Wilkinson noted that he and his colleagues were impressed by the students, highlighting their “professionalism and dedication to safety diving into the data before jumping to conclusions.” He added that “the excitement from our team to have new ideas, along with the energy these students brought, was contagious.”
For more information, contact Mayra Ramirez at ramirezm@iastate.edu or 515-520-3101.
Capstone Request Form: Complete this form to match your project with the most suitable academic department by sharing its goals, focus, and needs.