Due to an aging and limited workforce, Iowa’s small to medium-sized companies are experiencing the not-so-unique pain points of repetitive injuries, lower productivity caused by fatigue, decreased efficiency, and turnover. Exoskeletons are emerging as a significant advancement in workplace ergonomics, thus addressing these pain points. They offer a blend of human intelligence and robotic strength to enhance productivity and reduce physical strain. Implementing Exoskeletons could make you an employer of choice since it will be seen as an investment in your people.
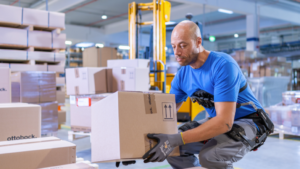
These wearable devices, which augment, enhance, or assist the user’s movements, are increasingly applicable in industries such as manufacturing and construction. They come in various forms, designed to support different body parts—upper body, lower body, mid body, or a combination of two. Exoskeletons operate on different actuation principles: passive, hybrid, or powered, with passive systems being the most common in industrial settings due to their affordability and simplicity. They can be considered as an entry point into automation. Some have used them as a stopgap during the automation process. It is easier and less expensive to implement, while other, more expensive automation solutions are designed and implemented. The cost to implement is a huge plus.
One advantage of implementing them is that they will help increase productivity due to the amount of effort the employee will need to exert will be reduced, thus reducing their fatigue level. A less tired employee will be able to work at a more consistent and efficient pace throughout the day. These employees will also benefit from wearing these devices in the form of the physical stresses placed on their bodies will be reduced. This can potentially reduce medical costs and productivity losses due to injuries. Research indicates the potential for substantial reductions in the physical force exerted by workers, promising a decrease in musculoskeletal disorders and significant productivity gains. With ongoing trials, including those done by CIRAS, concrete data is anticipated to highlight Exoskeletons’ benefits in stress reduction and productivity enhancement.
With advantages come disadvantages; there is no one-piece-fits-all solution. The environment and type of work being performed can limit the use and effectiveness of devices. The device must be fit to the job function being performed as well as the employee.
You can take advantage of what CIRAS offers by sending us videos of your processes for us to analyze free of charge. Another way we can help is through our pilot projects, you will be able to use one of our devices for a week allowing both the company and employee to evaluate if a particular device is right for them. To learn how Exoskeletons may be able to assist your company and to explore their potential benefits in reducing physical strain and increasing productivity, you are encouraged to contact Ty Hill for more detailed information and guidance. CIRAS can provide insights into how these innovative technologies can be tailored to meet your company’s needs, ensuring you leverage the latest advancements in workplace ergonomics.
For more information, contact Ty Hill at tyhill@iastate.edu or 515-357-4379.