A university might not be the first place a manufacturer would turn to for rapid parts testing, but that’s exactly what happened when Putco, a vehicle product accessory manufacturer in Des Moines, needed to evaluate the porosity of an aluminum vehicle part in a matter of days to secure a large contract.
“CIRAS works at the speed of customers,” says Adam Lathrop, a CIRAS strategic adviser. “I don’t think manufacturers always know we do have the flexibility to turn things around quickly. But we’ll do everything we can to accommodate them. When companies succeed, we succeed.”
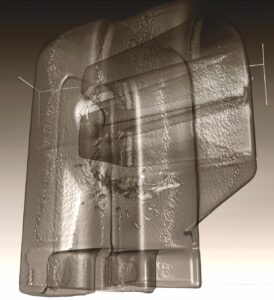
Putco had put out inquiries to private contractors to do industrial X-rays of cast aluminum units that it had purchased. They wanted to make sure these items met quality standards. All metal castings have some degree of imperfection, but with these, it was important to document that they didn’t have significant porosity that would compromise strength in critical regions.
CIRAS was the first to respond with a plan. “We were in a pickle, and CIRAS had visited us a couple of times, so we reached out to them,” says Nick Niemeyer, Putco engineer. “It’s paid off.”
CIRAS tested the pieces from Putco using its in-house X-ray equipment to generate a 3D-like file, computed tomography. This file can be manipulated to display virtual slices of the parts for evaluation, similar to a medical CT scan.
With this testing information, Putco secured a contract that increased sales by a million dollars retained another million in existing sales, and allowed the manufacturer to retain two positions.
“The priority of CIRAS is to improve the quality of life in Iowa by helping companies and their communities prosper and grow,” said Lathrop.
For more information, contact Derek Thompson at thompson@iastate.edu or 515-419-2163.