Lakeside Products has seen a substantial drop in the cost of producing door flaps for its pet doors despite the ever-increasing cost of raw materials. The savings is the result of a team effort involving the company, their mold supplier, and CIRAS.
“Our injection molding partner has had some challenges with the quality of a part they make for us,” said Bruce Beguhn, who owns the Polk City-based company. “They suggested a design change to improve the quality and reduce scrap and secondary labor, but we needed to know if it was truly going to be better than what we already have.”
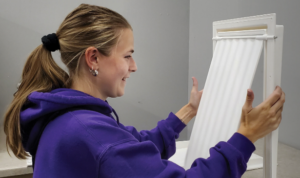
Beguhn shared the new design with Chris Hill, CIRAS engineering services director. Hill, who has extensive experience in injection molding, made some suggestions on changing the configuration of the design. He then brought in his colleague, John Roberts, CIRAS project manager, who did a Finite Element Analysis (FEA) of the new product to determine how it might behave.
“The primary concern was how the redesign might impact the strength of the part,” said Roberts. “In other words, would the new design solve the warping issue but create problems with cracks or breakage.”
Roberts first completed FEA simulations of the existing door to use as a design standard. He applied various loads and constraints to determine the door’s stress conditions. The same loads and constraints were applied to the new design and the stress results compared. CIRAS also provided a 3D printed prototype of the new component for marketing purposes.
“We did some adjustments based on stress analysis, but essentially we got it to the point where Bruce was comfortable that the new design would be structurally as strong as the original product but would be easier to mold with less defects,” Roberts said.
This project resulted in several additional benefits to Lakeside Products. There were decreases in manufacturing time to make the part and the amount of time needed to assemble the final product. The quantity of raw materials and scrap was reduced, and secondary work for out of spec parts was eliminated.
“When all those benefits are considered, we ended up reducing the cost of the product by 25% in spite of an increased cost in the raw material,” said Beguhn. “We couldn’t ask for better results than that.”
For more information, contact John Roberts at jarobert@iastate.edu or 515-294-0932.