For companies new to continuous improvement (CI) or in the early stages of building a CI team, Tony Hogan has five pieces of advice: choose momentum over perfection; get comfortable in the gray; know what problems you’re solving; bring everything back to business metrics; and make progress visible.
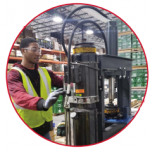
“Leave lots of space for learning,” said Hogan, president and chief operating officer of World Class Industries (WCI). “Good news can wait for me. Give me the bad news and then let’s talk about how we’re going to deal with it.”
WCI provides contract assembly and kitting to global OEMs like John Deere, Caterpillar, and Bobcat, and it also works with small- to medium-sized manufacturers. Headquartered in Hiawatha, the company has eight locations in the United States and one in Germany, as well as a workforce of about 250 people. And for Hogan, each one of those people matters and each contributes to the company’s success.
WCI is a member of the Iowa Lean Consortium (ILC). Jen Michael, WCI’s CI manager, credits their ILC membership with providing resources to improve business practices and stay current with trends in supply chain and manufacturing.
“They really embody the foundation of Lean, which is respect for people,” said Tracy Schuster, ILC program director. “They’re very transparent about their lessons learned and how they can grow as a team. Everything they learn flows right back into their overall strategy.”
For Hogan, CI is as essential to his company’s productivity and success as traditional business functions like finance, accounting, and human resources. The CI team is a key part of discussions and collaborations.
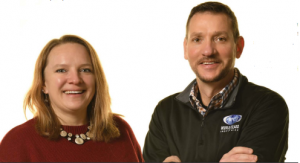
“Like other members of the leadership team, they help us clarify the problem, determine the data we need to measure the problem, and help with strategies to move forward,” Hogan said.
For more information, contact Tracy Schuster at tschust@iastate.edu or 515-715-0164.