Making relatively small changes to one aspect of your business
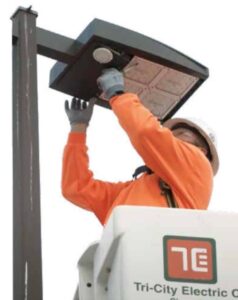
operation can make a big impact on productivity, your bottom line, and your culture.
That’s the lesson learned by Tri-City Electric, which saved an estimated $20,000 after spending just five hours with CIRAS project manager Emily Betz. She was called in to help the company organize their construction planning documents. As many as 400 hours a year were being wasted searching the company’s database for pertinent documents.
“They were keeping everything from lost bids to notes on current projects in the same file with no way of knowing which documents were relevant or the most recent,” said Betz. “So, we talked about where to keep documents, what to name them, and how long to keep them with a goal of finding better ways of organizing their information so everyone could get what they needed when they needed it.”
Tri-City Electric, based in Davenport, is one of the nation’s oldest and largest family-owned electrical contractors. The company serves the new construction, renewable energy, communications, audio-visual, electrical distribution, engineering, and integration and security needs of residential and commercial clients. With a workforce of nearly 1,500, keeping everyone informed and updated was challenging under their old system.
“Our server and document control were not as efficient as we wanted,” said Dave Aguirre, director of construction services. “Emily got us headed in the right direction by asking the right questions and getting us to focus on improving our processes and standards.”
The company had to let go of some of their old habits and embrace new ways of organizing documents. Betz said there was little resistance, which made the process move smoothly and quickly. Tri-City is a member of the Iowa Lean Consortium, so improving efficiency and eliminating waste were not unfamiliar concepts.
“They immediately made decisions and implemented changes right there in the room instead of saying ‘Maybe we need more discussion on this,’” said Betz.
The company didn’t stop there. They continued to bring more people “into the room” to look at how processes could be improved.
“This started a cascading effect in other areas,” Aguirre said. “It’s unbelievable how people are now working together from different departments on ways to improve. We have started our own internal lean coffee that has really taken off, and we are tackling other areas where we can improve as well.”
“The engagement has been a breath of fresh air, to be honest. I am very happy we took the first step in contacting CIRAS to help wrangle us in and get us heading in the right direction.”
For more information, contact Emily Betz at betze@iastate.edu or 515-567-0216.