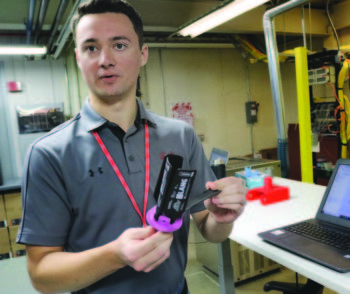
Craig Klocke believes machines one day will be much more efficient because an electronic eye will constantly be checking what they make.
Installing scanners at the end of a production line would allow manufacturers to continuously watch for the changes that come when cutting tools are wearing out, said Klocke, head of additive design and manufacturing for Danfoss Power Solutions in Ames.
“As tools wear, as machines wear, the scanning would allow the machines to adjust,” Klocke said. “You’d end up with a better product, and you’d know exactly when it was time to replace a part or tool. You’d have continuous adjustment of the process.”
Quality control is just one of the possible ways that Klocke believes 3D scanners could quickly help improve the manufacturing at Danfoss. After testing the technology with help from CIRAS, Klocke expects Danfoss to purchase its own 3D scanner later in 2020.
“CIRAS makes it really easy to evaluate the new technologies,” Klocke said. “This gives us a chance to see what could happen in those unique, one-of-a-kind situations where we can’t yet justify purchasing something by itself.”
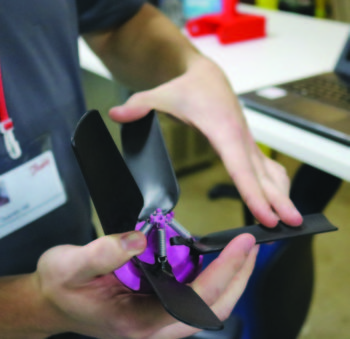
Last year, CIRAS worked with Danfoss to scan and reverse engineer some parts that frequently were breaking during a cleaning process. In another project, CIRAS helped the company define the digital model for a part and begin 3D printing the replacement itself—thereby saving weeks that previously were spent waiting for a new version to arrive.
Scanning technology is multifaceted, said Chris Hill, director of the CIRAS Technology Assistance Program. “If you don’t have designs for your components in a digital format, this is one way to get there,” he said. “We’re also working with the dimensional verification application. This could allow companies to understand part variation and see whether what they’re making or testing is really what they want.”
Scanning is becoming essential, Klocke believes, in helping manufacturers keep old-but-essential machines producing products. Some pieces you simply can’t afford to be without.
“In some cases, we only have 2D drawings,” Klocke said. “In some other cases, we don’t even have the drawing. Now the thing is broke, and we need to fix it. What are we going to do?”
Danfoss also is exploring the use of scanners as a test to quickly check what’s produced in its 3D printing hub. Such a process would allow the company to spot problems without waiting for something to be tested on the production line, Klocke said.
Those are just a few of the ideas that Danfoss is exploring involving the use of new technologies to improve the production process, Klocke said.
“We’re just getting started.”
> For more information, contact Chris Hill at chhill@iastate.edu or 515-313-8251.
A version of this article was published in the Winter 2020 edition of CIRAS News. To read more of that edition or others, please explore elsewhere on our website.