Sometimes, you just want to know.
Cline Tool, based in Newton, recently completed a 15-month project with CIRAS to evaluate its safety plans and procedures. The result? Cline now has a new Safety Committee to address safety procedures, processes, and compliance moving forward. And its Board of Directors is much more confident after being reassured that Cline has a strong program in place that meets OSHA requirements.
Jason Benson, Cline Tool’s chief financial officer, said the company turned to CIRAS to “get a realistic view of where we’re at with our safety program.”
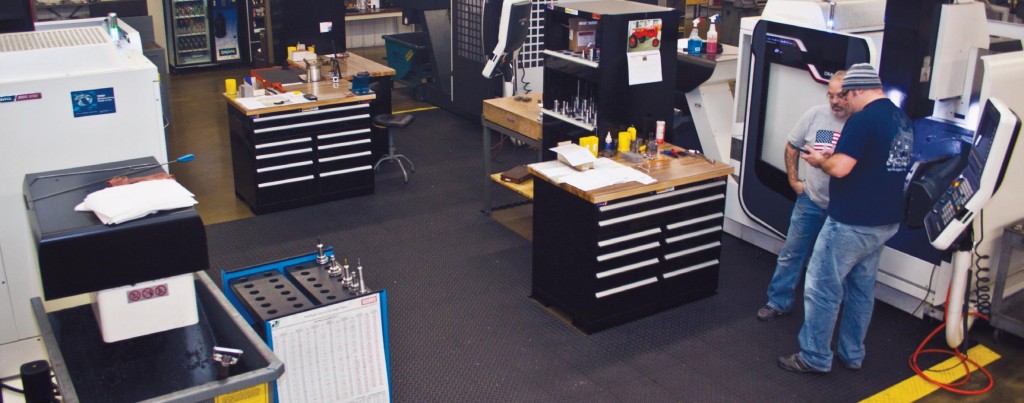
Jim Poe, CIRAS project manager, said the goal of safety transformation planning is to guide companies through a maze of regulations and “to help manufacturers provide a safe working environment for their associates.”
Poe started the process by walking through Cline Tool’s manufacturing plant and making assessments through the eyes of an OSHA inspector. “He saw where we might have challenges to overcome, which laid out the framework for our sessions,” Benson said.
The 12-session program involves assessing current conditions, document practices, emergency action plans, job hazards, and trainings. Poe also reviews topics such as storage of flammable liquids, machine guarding, electrical safety, indoor air quality, and other items specific to the location. Companies move through the program at their own pace, usually over a period of 12 to 18 months.
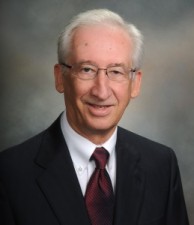
“Jim helped us to break the work down into manageable pieces,” Benson said. “He gave us relevant federal guidelines to follow and how that translates into real-world documentation and processes.”
As a result, the company has initiated regular safety walks by Safety Committee members to identify and resolve potential issues, completed Job Hazard Analysis documents for all shop positions, and refined its lock-out/ tag-out procedures. Cline also started a new safety training process for new hires, created an annual safety training schedule for existing employees, and added eye-wash stations throughout the shop area.
“We all felt like we had a safe shop … but we realized just how many areas could use some improvement,” Benson said. CIRAS was flexible and anxious to share its knowledge, he added.
“Any manufacturer could find a lot of value in a program like this.”
> For more information, contact Jim Poe at jrpoe@iastate.edu or 515-290-1398.
This article originally appeared in the Fall 2015 edition of CIRAS News. You can find the rest of this issue and more of CIRAS News on our website.