In a business environment where adoption of technology is increasingly important—but also increasingly overwhelming—CIRAS is helping Iowa businesses identify the best systems and reduce the risk of adopting those systems.
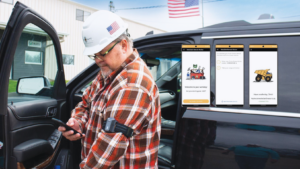
A case in point is Osmundson Manufacturing in Perry. Osmundson makes agricultural tillage equipment. It is a constant challenge to prevent soft-tissue injuries and the adverse effects of environmental factors, like dust and heat.
“We saw an opportunity to help them understand the physicality that was being imposed on their operators,” says Chris Hill, CIRAS engineering services director.
CIRAS connected Osmundson with MakUSafe, which manufactures a sensor workers can wear on their arm that is designed to improve worker health, safety, and productivity while reducing incidents and mitigating workplace hazards and risk exposures.
At first, Osmundson was skeptical. They were concerned about the usefulness of the data, having the time to evaluate the data, and getting buy-in from the workers who would need to wear the sensor.
Osmundson bought one system with enough sensors for all employees on one shift. Within a few months, Osmundson ordered enough systems to cover the remaining shifts. Heather Bruce, President and CEO of Osmundson, was impressed with the astounding amount of data they were given, including trends over time, and how easy it was to interpret the data and make real-time changes.
One worker, for example, was experiencing shoulder pain from repeat motion with a hammer. He got feedback from the sensor on how he could use the hammer differently, and now he knows he doesn’t have to simply hit harder, but can do it in a way that puts less stress on his shoulder.
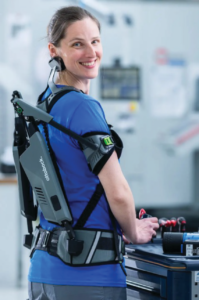
It’s a natural fit for a company like Osmundson, and Gabe Glynn, MakUSafe CEO, says they might not have connected with Osmundson if it hadn’t been for CIRAS. He said he appreciates how CIRAS connects technology companies like his with manufacturers.
In other cases, CIRAS can help companies make initial forays into using technologies that reduce injuries and increase efficiency.
In the case of Rosenboom Machine & Tool in Sheldon and Spirit Lake, CIRAS helped them experiment with exoskeletons, a type of hi- tech brace that provides body support to reduce fatigue and injuries. In the case of Rosenboom, they tried a particular exoskeleton with industrial painters who at times hold spray attachments above their heads, which can lead to fatigue and strain.
CIRAS can de-risk technology adoption for companies by helping them understand the capabilities and limitations of various technologies. CIRAS helps them conduct pilots before making a purchasing decision.
“Working with CIRAS gave us the opportunity to try the technology in our working environment,” said Kevin West, environmental health and safety coordinator at Rosenboom.
In today’s competitive workforce environment, it’s critical that manufacturers explore ways that technology can make jobs more attractive and reduce injuries. “Companies want to become employers of choice, and technology can help reduce costs and improve the work life of their employees,” said Hill.
For more information, contact Chris Hill at chhill@iastate.edu or 515-313-8251.